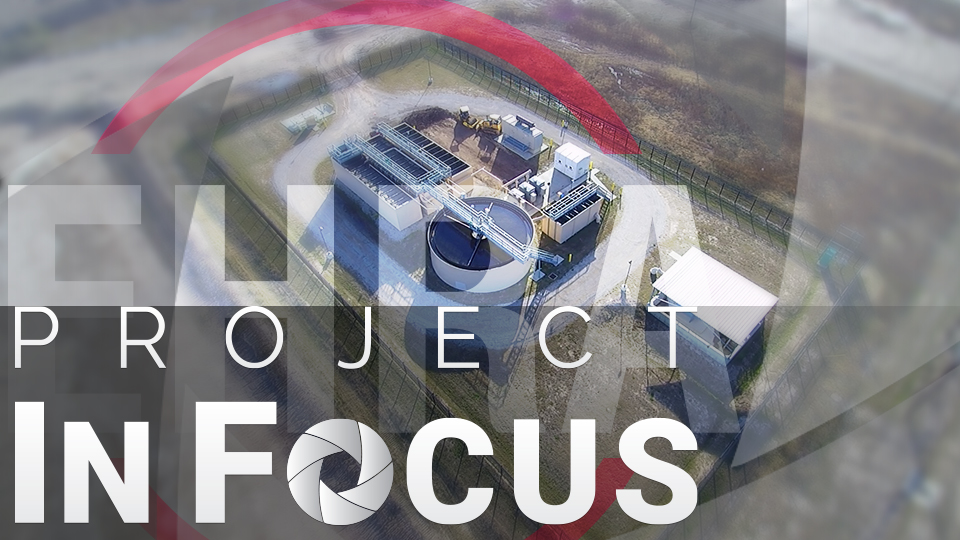
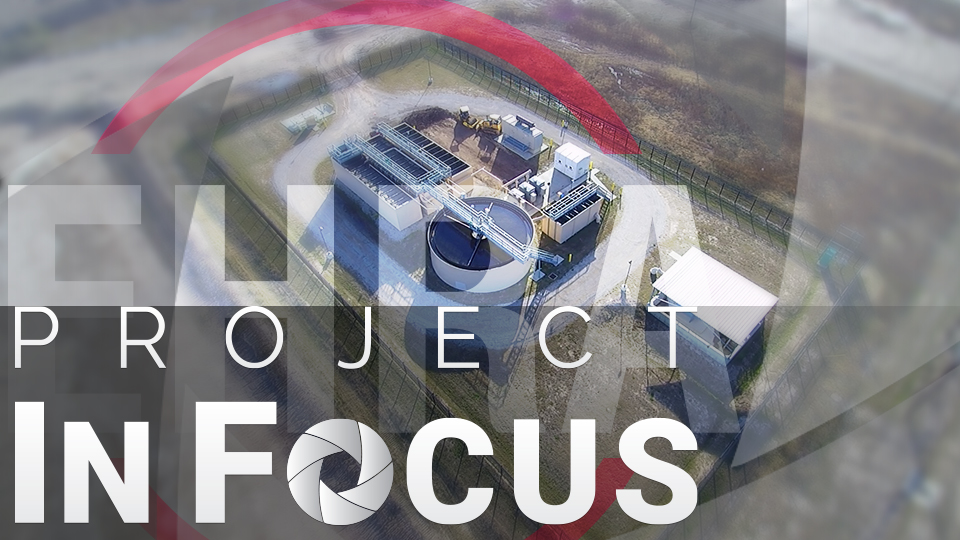
Identified as a top priority during the development of the District’s Parks Master Plan, this portion of trail was the first phase of over two miles of planned trails to provide connectivity and recreation for District residents.
The purpose of this project was to convert the existing at-grade crossing of Brazoria County Road 56 (CR 56) and State Highway 288 (SH 288) into a diamond interchange that includes a new overpass bridge. Coordination with TXDOT, area landowners, utility companies, and Brazoria County was integral in obtaining approval and acceptance of the project.
This project was the second phase of parks implementation outlined in the District's Parks Master Plan, which was completed by EHRA in 2007. Utilizing the site of a recently demolished former wastewater treatment plant provided an opportunity to create a passive park space for District residents.
EHRA conducted a traffic engineering study to identify the impacts of a proposed master development located near the intersection of FM 1488 and Peoples Road in the City of Conroe.
EHRA performed preliminary drainage area delineations for nine creek crossings and calculated approximate 100-year flows for each culvert crossing. Culvert structures were sized for each of the six crossings, ranging from 48” round pipe culverts up to dual 5’x5’ box culverts.
The existing Harris County Municipal Utility District 536 (HCMUD 536) wastewater treatment plant (WWTP) required expansion to accommodate significant growth in the area, especially from developments such as Camillo Lakes, Marcello Lakes and Treviso Gardens. EHRA was contracted to provide final engineering plans, survey services, bidding process support, construction phase services and project site observation. The Phase III WWTP expansion design kicked off in May of 2019, contractors were solicited in June 2020 and construction started June 2021. EHRA Facilities Practice Area Leader Paul Anderson, PE, served as project manager for this vital upgrade to the HCMUD 536 amenities, located in the Katy area of Greater Houston.
One interesting component of the project was the specialized type of wet well and the coordinating in-ground splitter box EHRA designed to support it. The wet well was utilized to split the raw wastewater flow between the existing plant and the expansion plant. To control the flow between the two plants, EHRA revised the original V-notch weir splitter box design and instead integrated short-crested triangular weirs, which can be fabricated entirely out of concrete. This specific design element was unique in that it both minimized the maintenance needs of the control structure and facilitated a water-tight connection with the knife gate. The innovative splitter box design ensures maximum and precise operator control over actual flow and flow measurements.
The Covid 19 pandemic introduced supply chain challenges throughout this project that EHRA expertly found ways to surmount without sacrificing quality. For example, steel supply shortages inspired the use of refurbished and prefabricated tanks rather than custom-built tanks. Deployment of these tanks also saved the client time (that building custom tanks would have required) and money by avoiding the absorption of steel price increases resulting from widespread shortages. Additional substitutions that saved time and money included alternate electrical equipment as well as revised pipe materials and sizes.
Another challenge overcome involved the plant membrane filter, which was previously damaged (and thus off-line) due to flooding and freezing temperatures during Winter Storm Uri. The membrane filter is critical to the overall water treatment process as it “polishes” the water leaving the plant. EHRA coordinated closely with the plant operator, construction contractor and the membrane filter manufacturer to discover techniques that ultimately rehabilitated the filter and returned it to its original functionality and weather resistance.
Naturally, teamwork amongst members of various EHRA practice areas was critical to seamless project execution. The EHRA Construction Phase Services (CPS) team was particularly involved in the successfully delivery of Phase III of the HCMUD 536 WWTP Expansion. Alex Borja and Frank Ontiveros facilitated project site observation, effectively keeping the project pressing forward and maintaining the prescribed schedule. Their combined experience as operators offered invaluable insight into both plant design and construction. Jason Keeling, also with the EHRA CPS group, offered stellar construction management, and Nicole Davis masterfully juggled all project paperwork, from bid documents and contracts to pay applications. Further, Carlos Flores, PE of EHRA’s Structures practice area contributed important feedback on the project splitter box design, evaluating and reviewing each design amendment.
While this project expanded upon an existing WWTP, the overall effort required a complete design, as the expansion was conceived as a second treatment train. As project engineer, this was my first wastewater treatment plant design, so I thoroughly enjoyed the opportunity to experience the entire process from start to finish. I learned so much that I can now apply to future projects of a similar nature.
Due to productive coordination with leaders at HCMUD 536, with skilled external partners such as RJ Construction and with internal collaborators at EHRA, construction of this project is currently complete, and the plant is fully operational. The final construction cost was approximately 2.1 million dollars.