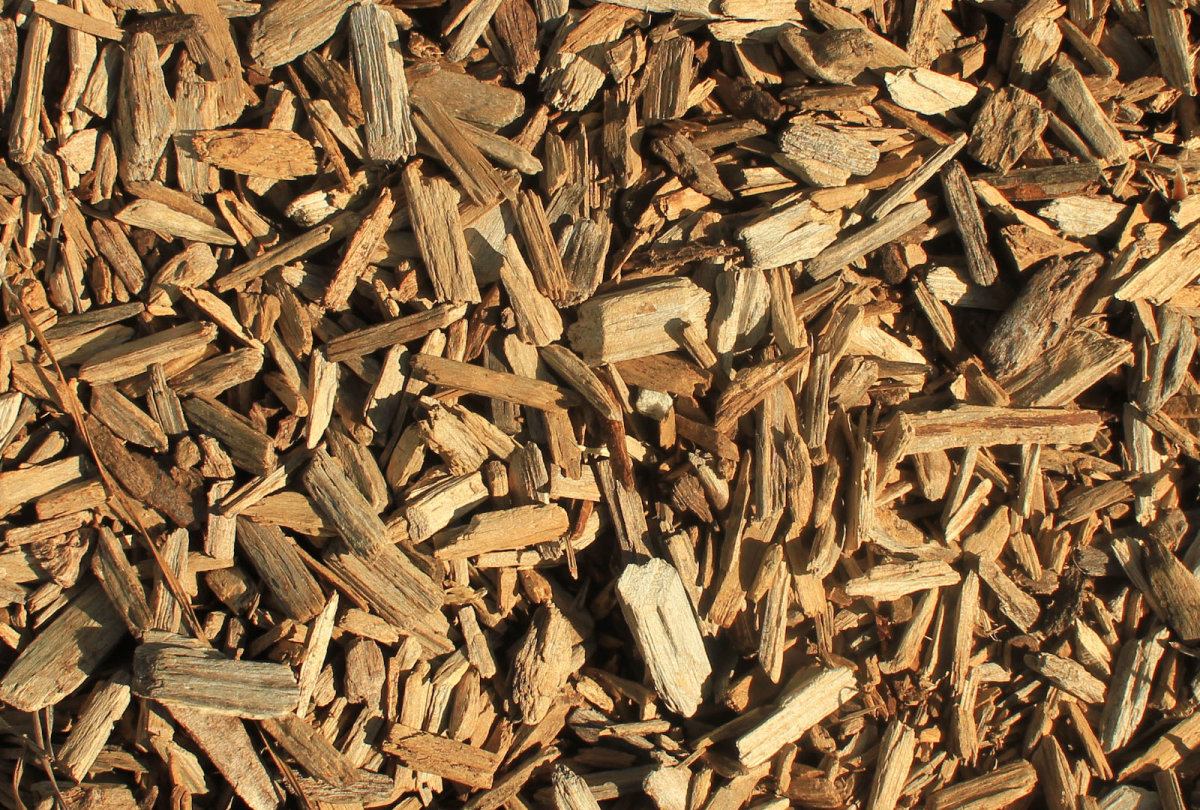
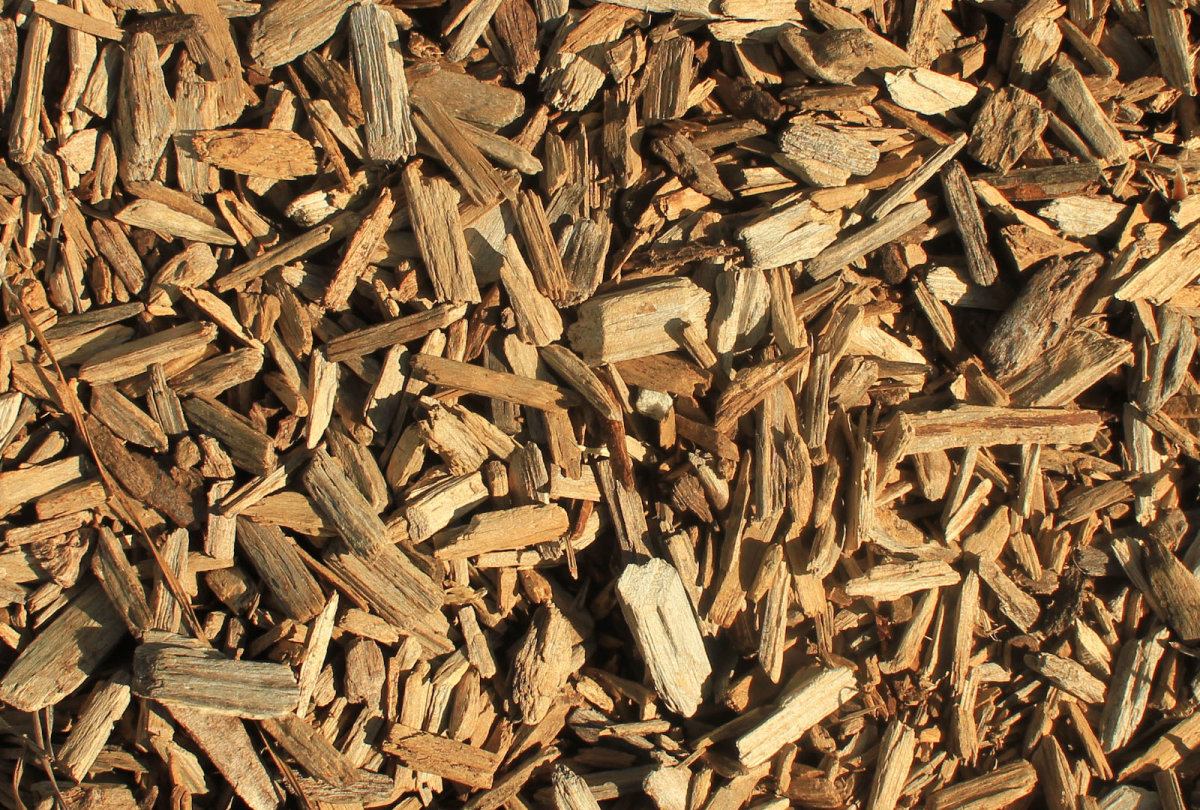
The purpose of this project was to convert the existing at-grade crossing of Brazoria County Road 56 (CR 56) and State Highway 288 (SH 288) into a diamond interchange that includes a new overpass bridge. Coordination with TXDOT, area landowners, utility companies, and Brazoria County was integral in obtaining approval and acceptance of the project.
This project was the second phase of parks implementation outlined in the District's Parks Master Plan, which was completed by EHRA in 2007. Utilizing the site of a recently demolished former wastewater treatment plant provided an opportunity to create a passive park space for District residents.
EHRA offered its Landscape Architectural services to complete a Parks and Trails Master Plan for the District.
A 720-acre gated master planned community located off Telge Road, just north of Willow Creek. See how EHRA was involved in this project.
EHRA was selected as one of two firms to provide professional surveying services under contract to Houston Community College System.
Striking just the right balance between softness and sturdiness, balsa wood is a choice material for crafting anything from model airplanes to full-size wind turbine blades. Scientists in the United States and China have opened up a new realm of possibilities for balsa by hijacking its natural structure with chemical and physical treatments to transform it into a "wood carbon sponge" capable of enduring repeated compression and other extreme mechanical conditions. Their work appears March 1 in the journal Chem.
"Our results reveal that rigid and incompressible balsa can be made highly compressible by a chemical treatment and carbonization process, yielding a wood carbon sponge with mechanical compressibility and fatigue resistance and electrical response sensitivity surpassing those of most reported compressible carbonaceous materials," says co-senior author Liangbing Hu, a nano-engineer and materials scientist at the University of Maryland, College Park (UMD)'s A. James Clark School of Engineering. "Since this wood carbon sponge is fabricated completely from natural wood with a simple and cost-effective method, the source material is also exceptionally renewable and sustainable, as opposed to popular options like carbon nanotubes or graphene."
The authors achieved the bendable yet resilient architecture of the wood carbon sponge by using common chemicals to destroy the stiff hemicellulose and lignin fibers that maintain the normal cell-wall structure of the balsa wood and then heating the treated wood to 1,000?C in order to turn the organic material into carbon alone. The net effect of the process was to collapse the repeated, regular, rectangular pockets typical of the microstructure of balsa and other woods and replace them with a stack of wavy, interlocking, arch-like carbon sheets, likened by Hu to a cross between a coiled spring and a honeycomb.
Whereas normal carbonized wood, obtained from only the heating step without any chemical modifications, is so fragile that any reasonable applied force pulverizes it irreversibly into ash and dust, the wood carbon sponge withstood and rebounded from substantial compression for up to 10,000 consecutive trials before deformation set in. Such a performance initially surprised the research team, which was also headed by Teng Li, a mechanical engineer at the University of Maryland, College Park, and Jia Xie, an electrical engineer at the Huazhong University of Science and Technology (China).
After conducting further mechanical and electrical tests on the sponge, the researchers were able to incorporate a slice of it into a strain sensor prototype suitable for attachment to a human finger, a quality desirable for use in wearable fitness or health-monitoring electronics.
The researchers believe that the wood carbon sponge material could also be incorporated into water-purification devices and energy storage and conversation technologies, such as supercapacitors and rechargeable batteries. "The abundant applications illustrate the value of a strategy that explores the hidden potentials of natural materials, such as trees, by drawing inspiration from other natural structures and sources," Hu says.
This work was supported by the Maryland NanoCenter.
Source: Science Daily