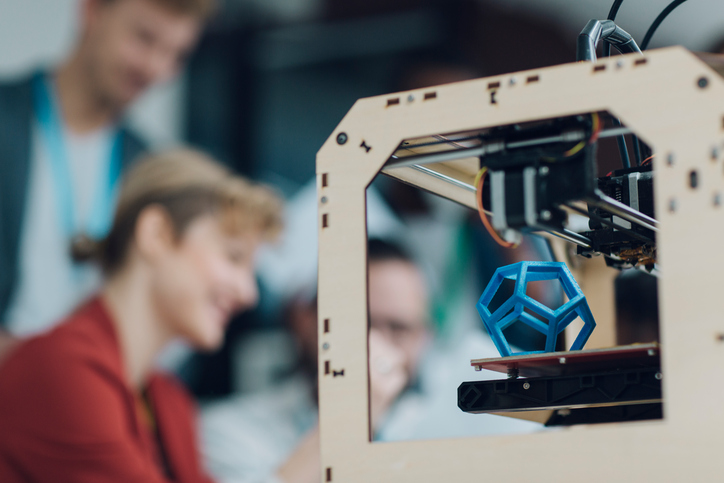
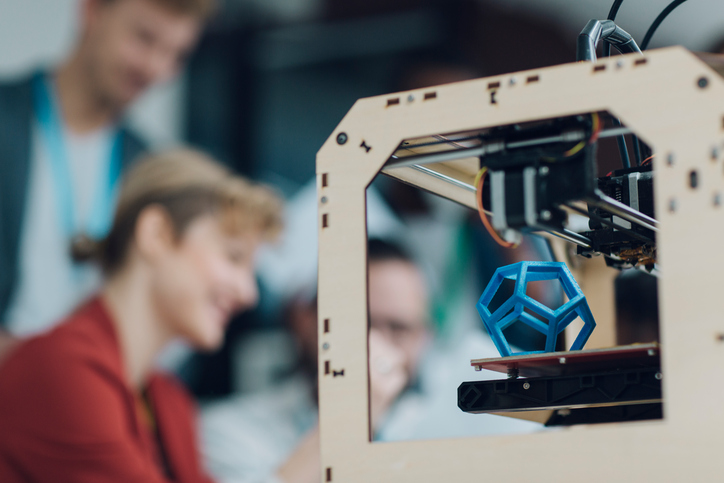
EHRA worked with the District to create a comprehensive Parks Master Plan, which included recommendations for the development of over two miles of hike/bike trails adjacent to local streets, and within flood control and utility pipeline easements. The District began implementation of the Plan by prioritizing the beautification of West Road, a major arterial street that runs through the District.
This project was the second phase of parks implementation outlined in the District's Parks Master Plan, which was completed by EHRA in 2007. Utilizing the site of a recently demolished former wastewater treatment plant provided an opportunity to create a passive park space for District residents.
The new roadway design comprises of one-half major thoroughfare, conventional drainage, a 600-ft long bridge over Willow Fork Bayou, Retaining walls and intersection improvements at FM 1463 (including traffic signals and illumination).
Identified as a top priority during the development of the District’s Parks Master Plan, this portion of trail was the first phase of over two miles of planned trails to provide connectivity and recreation for District residents.
EHRA designed an expansion that implemented the installation of a new triplex lift station operating in conjunction with the existing duplex lift station.
What if your home was built by a 3-D printer? As concrete is fed into the printing device, a technician hits enter on her computer and a 3D printer starts fabricating the structure’s walls and roof. The final product will be created almost entirely by preprogrammed software and a movable printer injecting concrete, with no need for human construction workers. This isn’t science fiction, it’s a reality on the cutting edge of construction and technology.
The use of 3D printers in the construction industry will have legal implications that will affect owners, contractors, manufacturers and software developers.
The additive manufacturing boom has reached the construction industry and will certainly impact the way construction projects are managed. The rise of 3D printers will translate into fewer workers on construction sites, as printers will be automated and largely autonomous. Projects will be completed faster, as 3D printers will be capable of working at all hours, and will not require overtime.
Current concrete-injection 3D printers developed by WinSun Decoration Design Engineering, in China, have the capacity to print small houses, including walls and roofs, at a pace of up to 10 small houses in 24 hours.
3D printing capabilities go beyond just concrete. The team of MX3D, in Amsterdam, is currently working on delivering the first completely 3D-printed steel bridge. U.S.-based Contour Crafting is developing 3D and autonomous construction technologies that would allow for the construction of tall concrete towers, such as wind turbines, using climbing robots that would "print" the contour of the structure as they move upward.
Developers have positioned 3D printers tailored to the construction industry to work almost like robots. That is, the 3D printer is not just printing a door or a beam that will later be installed by construction workers, although that capability certainly exists, it is effectively installing the printed component in-place.
However, innovation and disruptive technology bring new legal risks and implications. In the context of construction defects claims, 3D printers will expose manufacturers and developers to liability and claims that would normally be attributed to human error.Instead of human workers building a structure, a 3D printer will additively manufacture it after a pre-generated plan is uploaded to the printer’s software. How will liability be apportioned when the finished structure is found to have cracks, be uneven, improperly thick or have the wrong finish?
Whether the 3D printer is owned by the contractor, is being leased as equipment or is the equipment of a subcontractor will affect who can be found liable.If the defect is the result of the printer’s malfunction, the contractor will have warranty and indemnity claims against the manufacturer arising out of privity from purchasing or leasing the 3D printer.If the defect is the result of a software malfunction, that could open the developer to negligence and warranty claims for the value of the defects in the project at issue.If there is an independent technician, acting as a subcontractor, feeding the plans into the 3D printer could also be open it to liability if the defect was the result of improperly uploading those plans or operating the 3D printer.
In addition to claims against the contractor, the owner could also have claims against the manufacturer or software developer for economic loss, even in the absence of direct privity, if the owner can show the damage to his property caused by the 3D printer was foreseeable.
When faced with a construction defect caused by a 3D printer used by the contractor or one of its subcontractors, the owner will certainly have, at the very least, an argument that the manufacturer of the printer or developer of the software should have been aware that a malfunction of its hardware or software would, in turn, impact the owner’s property.
Increased prevalence of this emerging technology will also have an impact on material suppliers. If 3D printers will be used in a specific project, designers and contractors should provide proper specifications for material compatible with the specific 3D printer. Material suppliers will also have to certify their materials as compatible with the printers.
Failure to do so could open designers and material suppliers to liability for construction defects resulting from the incompatibility of the material with the specific 3D printer.
The use of 3D printers in construction projects is also likely to conflict with current licensing and permit regulations.
As the use of 3D printers becomes more common, government agencies in charge of inspecting construction projects will have to adapt to the faster-paced construction offered. In the ideal scenario, governmental agencies would embrace the new technologies in the construction industry and, for example, invest in automated scanner drones that could inspect an automated 3D printer’s work and, immediately thereafter, send the inspection’s result to the governmental agency for certification.
Such advances, however, may be difficult to achieve unless states, cities and counties make significant investments in infrastructure.
As 3D printers/robots become more commonplace on construction projects, contractors should be mindful of including express warranty clauses in purchase and leasing contracts for 3D printers.
Designers and material suppliers will have to confirm that construction materials under plans and specifications will be compatible with 3D printers; and governmental agencies will have to adapt to the fast production rate of 3D printers.
Source: http://enr.com